The PlantPAx system helps producers make better, faster process control decisions and enables them to respond more quickly to the demands of customers and fast-changing specifications. The latest system release has been designed to be an integral part of a digital transformation strategy, helping companies be more productive and profitable while reducing operational risk.
Rethink what a modern DCS can do
Many producers are adept at navigating the complexities and challenges of staying competitive. This is true in a variety of industries ranging from packaged consumer goods including food and beverage, to mining, oil and gas and power generation. That’s why it’s so important to implement the latest technological advancements to continue the ever-evolving digital transformation journey.
From the control room to the board room, process system users face the persistent challenges of balancing productivity against budget and resource constraints, as well as proactively addressing evolving operational risks. The PlantPAx 5.0 DCS helps companies to meet these challenges and experience real productivity gains in all areas of the plant.
PlantPAx 5.0 ensures that plant-wide and scalable systems drive productivity, improve profitability, reduce overall risks and positively impact the lifecycle of plant operations.
Do more with less to impact the bottom line
Production teams must do more with less to meet budget expectations throughout their plant’s lifecycle. The allocation of approved capital or operational funds must demonstrate a positive return regardless of the scale of investment. Whether tasked with supporting an existing infrastructure or designing a next-generation facility, teams must excel with limited access to resources.
A modern DCS
The PlantPAx system utilises a common automation platform for seamless integration between critical process areas and the balance of the plant. It connects process, discrete, power, information and safety control into one plant-wide infrastructure, increasing efficiencies and productivity across all layers of operations. This eliminates disparate control systems and results in significant optimisation improvements, helping to reduce total cost of ownership.
A modern DCS provides a wide range of architecture options for increased flexibility. The same platform can be used for single stations or large distributed architectures. It also offers scalable system capabilities — HMI, batch management and data collection that does not require extensive architectures — perfect for process skid equipment and rapid integration.
PlantPAx 5.0 is based on secured, open communication standards leveraging EtherNet/IP as its backbone. As a result, real-time information is readily available throughout the enterprise for better business decisions. It helps improve productivity by delivering production intelligence and visibility into enterprise level systems, helping to drive efficiencies.
In addition, PlantPAx 5.0 allows the use of commercial off-the-shelf hardware and supports the adoption of the latest IT technology that improves productivity. It addresses industrial security from the individual device on the plant floor to the enterprise level.
Improving productivity, driving profitability and reducing risks
Process functionality native to controllers, cyber-secure architectures and improved availability support the lifecycle needs of plant operations in a variety of industries.
Robust architectures: Process built controllers extend the Logix family with cutting-edge processing power and capacity to reduce the complexity of PlantPAx architectures. Rockwell Automation’s approach to process control creates a unified experience from skid to plant to multi-site, which reduces the total cost of ownership throughout the lifecycle of the system.
Project consistency: With native process instructions embedded in the controller firmware, project teams can adopt approaches to control strategies that drive consistency across projects. A consistent approach simplifies the lifecycle management of deployed systems as teams modernise their automation infrastructure.
Streamlined workflows: With improved design and operational user experiences, development teams realise savings in the configuration of instrumentation, alarms and diagnostic system elements. Operators have the extended ability to view underlying control logic in a safer and secured manner. Maintenance teams will have improved workflows for system troubleshooting to reduce downtime.
TÜV-certified for cybersecurity: To operate at peak performance and minimise cybersecurity threats, PlantPAx system architectures are TÜV-certified to the international standard ISA-99/IEC 62443-3-3, which provides guidance on the implementation of an electronically secured system.
Analytics enabled: Process end users recognise the value of analytics as an essential strategy to realise profit in their process operations. PlantPAx 5.0 has purpose-built frameworks that easily connect live and historical data from the DCS into reporting and analytical tools. Frameworks enable extended experiences, such as augmented reality, using workflows aligned with process strategies controlling plant operations. Rockwell’s system allows companies to adopt a scalable analytics strategy by leveraging predictive and prescriptive models for process applications such as soft sensors, anomaly detection, or model predictive control. This provides teams with the digital transformation opportunity to improve uptime, reduce waste and drive overall profitability.
Read more about the benefits of the PlantPAx 5.0 DCS.
What is new about PlantPAx 5.0?
The newest release of PlantPAx offers more valuable technical features than ever before. From embedded alarms and the new native objects library to HiHART and SAMA instructions, the demo videos in this playlist will walk operators and engineers through specific features. Each video gives a glimpse into the new features within PlantPAx 5.0 and illustrates how this latest release can help drive out an impactful bottom line.
For further information on PlantPAx 5.0 and other Rockwell Automation products, please call your local NHP Account Representative or email us:
Australia: 1300 NHP NHP nhpsales@nhp.com.au
New Zealand: 0800 NHP NHP sales@nhp-nz.com
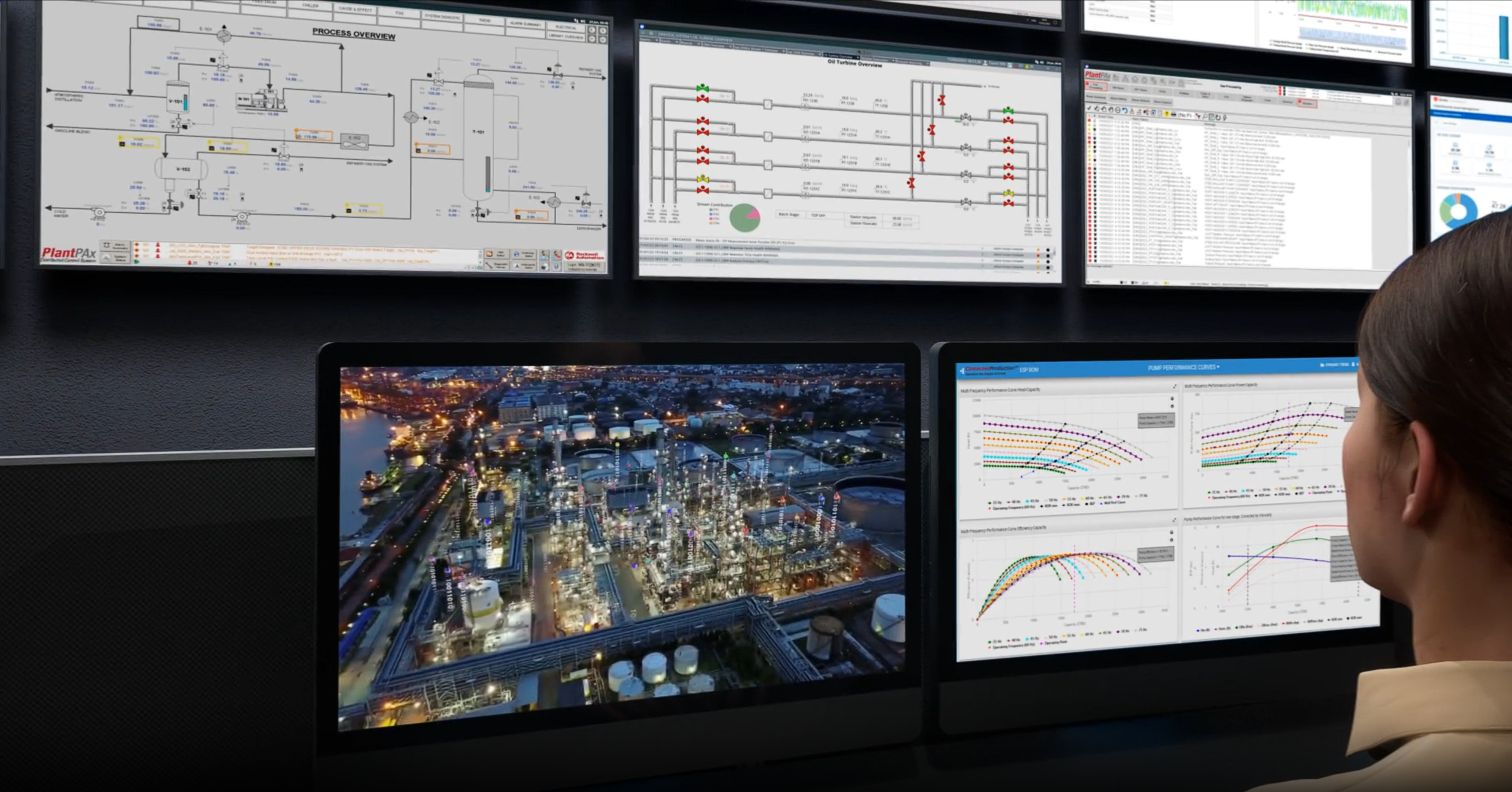